Energy Savings that Improve Your Bottom Line!
The Project
Management was concerned that current production operating practices might be inefficient and significant energy saving opportunities existed.
The customer’s manufacturing facility produces various molded fiber cartons. The plant utilizes recycled newspaper as their fiber feed stock and the factory has three production lines that produce various carton configurations. The rate of production for Dryer #1 was measured by paper kg/hour. The amount of water the dryer evaporated was approximately 2,270 kg/hour. The dryers required regular cleaning to remove condensate which appeared to be some form of hydrocarbon and the capacity was below specifications.
“Hiring the experts will save you thousands in energy costs”
– Russ Chapman, President, Firebridge Inc., 2019
The Firebridge Solution
Using the Six Delta™ Method to gain an optimised perspective, Firebridge identified several performance improvement opportunities. The Six Delta™ Method is a comprehensive approach through a systematic analysis which considers improvements over six interdependent focus areas. This method is data driven by metrics from each focus area which combine to drive a strong business case.
The Six Delta™ focus areas for this project are:
Primary: Energy Consumption – Product Quality – Process Production – GHGe Emissions
Secondary: Safety & Compliance – Equipment Reliability
Diagnosis and Findings:
A natural gas consumption baseline was developed to benchmark the dryer operating efficiencies. A temperature profile was then developed for the dryer and end product.
- Poor air and temperature distribution
- Poor de-watering on molding machine
- Problems with exhaust
- Poor dryer pressure control
- Excessive mold release oil contributing to external condensation
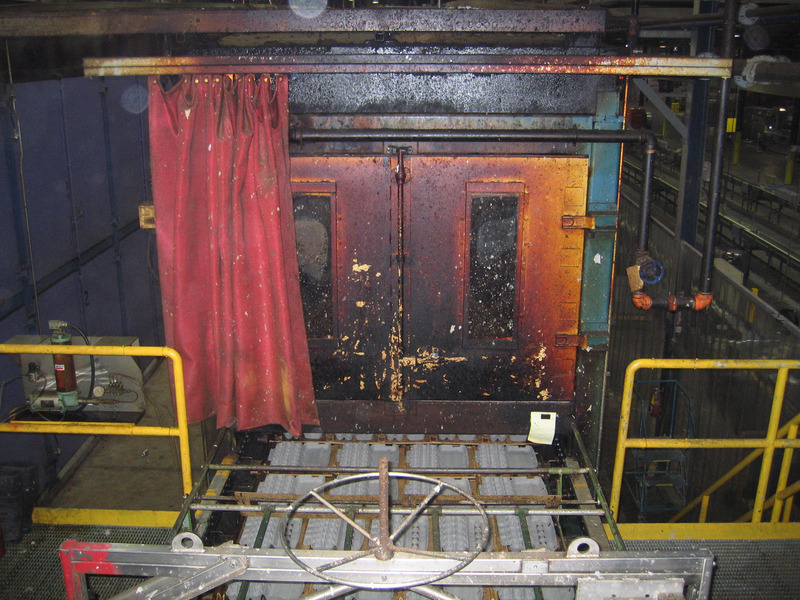
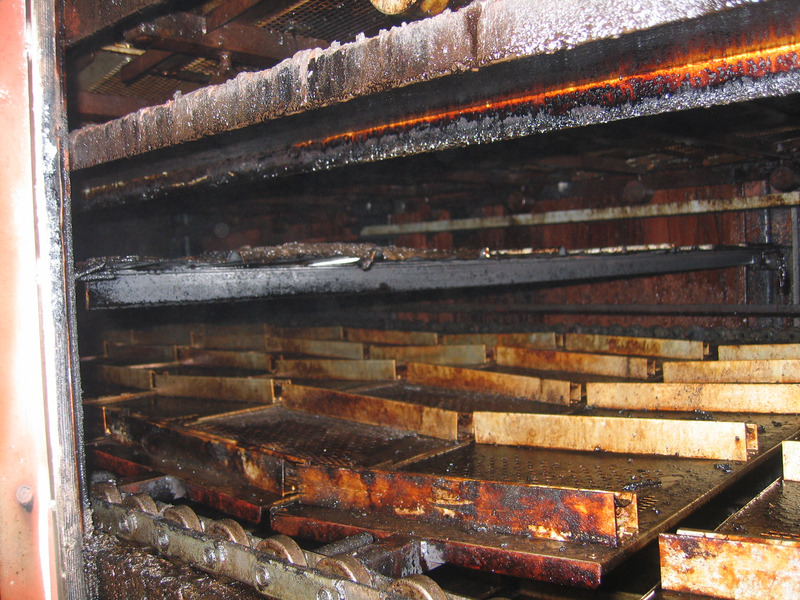
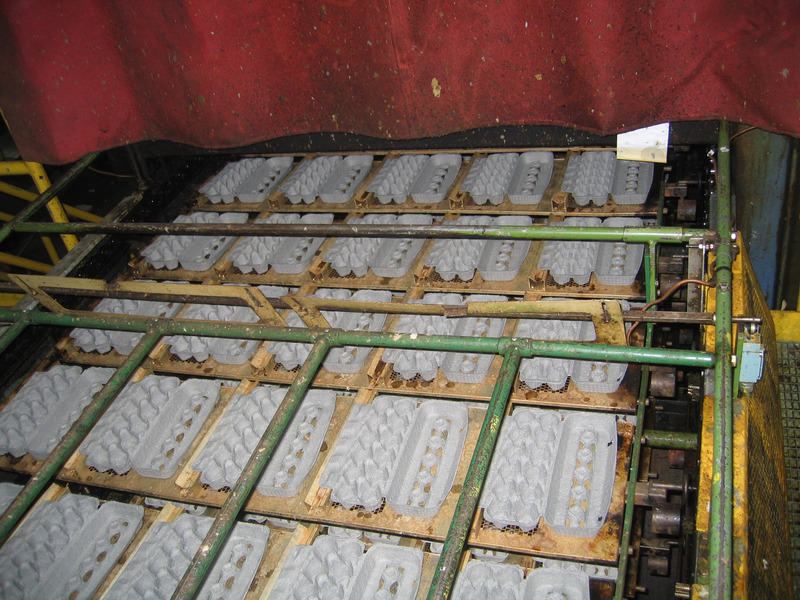
Improved results were found across all Six Delta™ focus areas.
Safety & Compliance
- Hydrocarbon condensate problem eliminated
Quality
- Modified oven design improves air balance and heat distribution
- Annual mold release oil savings of $60,000
Productivity
- Dryer throughput increased by 20%
Energy Consumption
- Annual fuel savings of $182,000
- Payback in less than 1 year
Reliability
- Lower maintenance, less product loss
Greenhouse Gas Emissions
- GHGe emissions reduced
Dryer and Product Temperature Profile
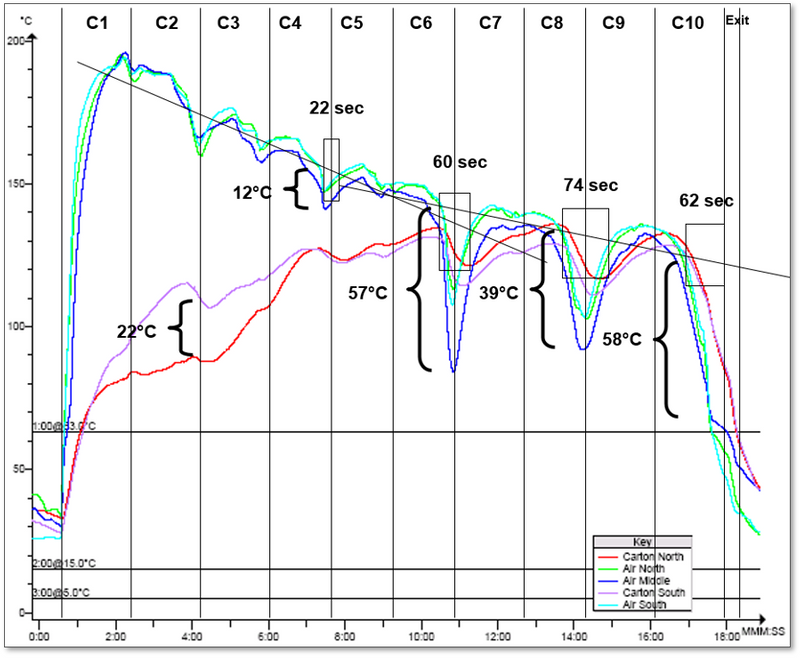
Liked what you read? Stay up to date with new content by Subscribing below!