Is Your Heat Treatment Furnace Draining Your Operating Profits?
The Project
There was a concern that fuel consumption as a percentage of cost was higher than the industry average and that significant energy saving opportunities existed. Having one of the largest furnaces in North America at 82 ft long, the customer specializes in heat treating very large or complex components. The furnace can operate up to 2000°F and has a maximum rated capacity of 400 tons.
A natural gas consumption baseline was developed to benchmark current furnace operating efficiencies. Energy saving strategies and priorities were determined through a systematic analysis of the existing equipment.
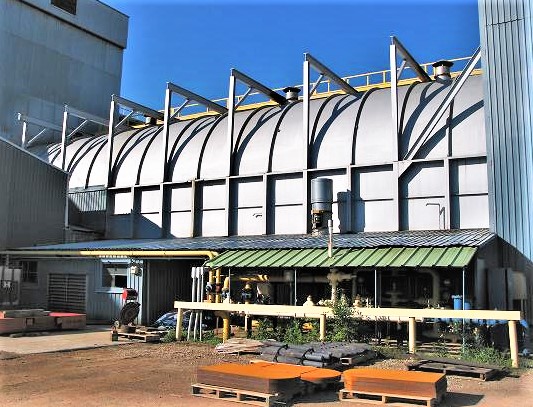
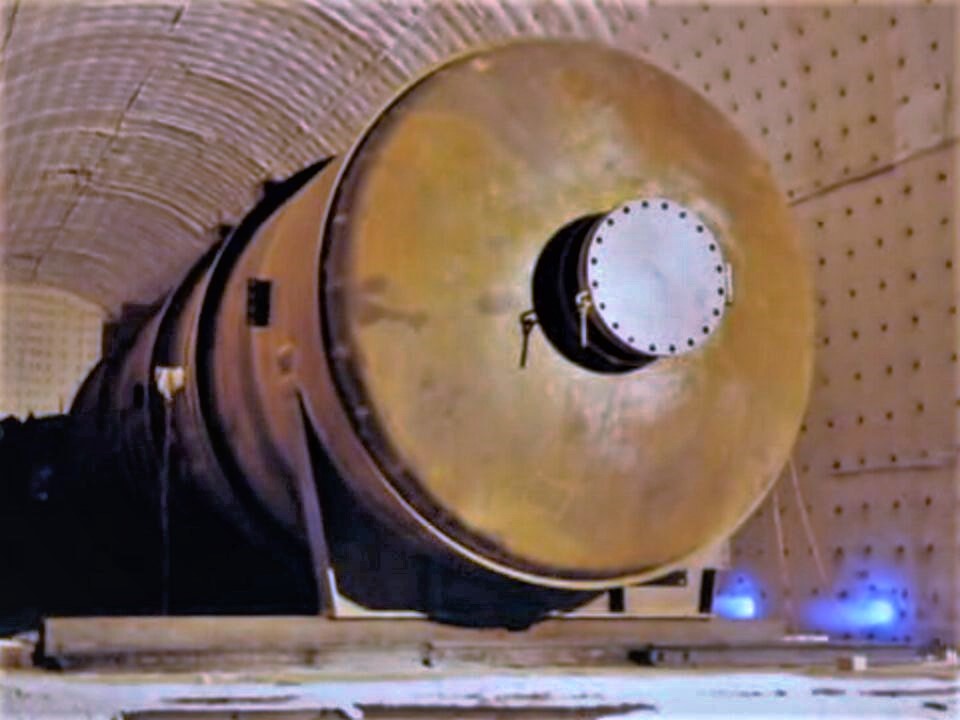
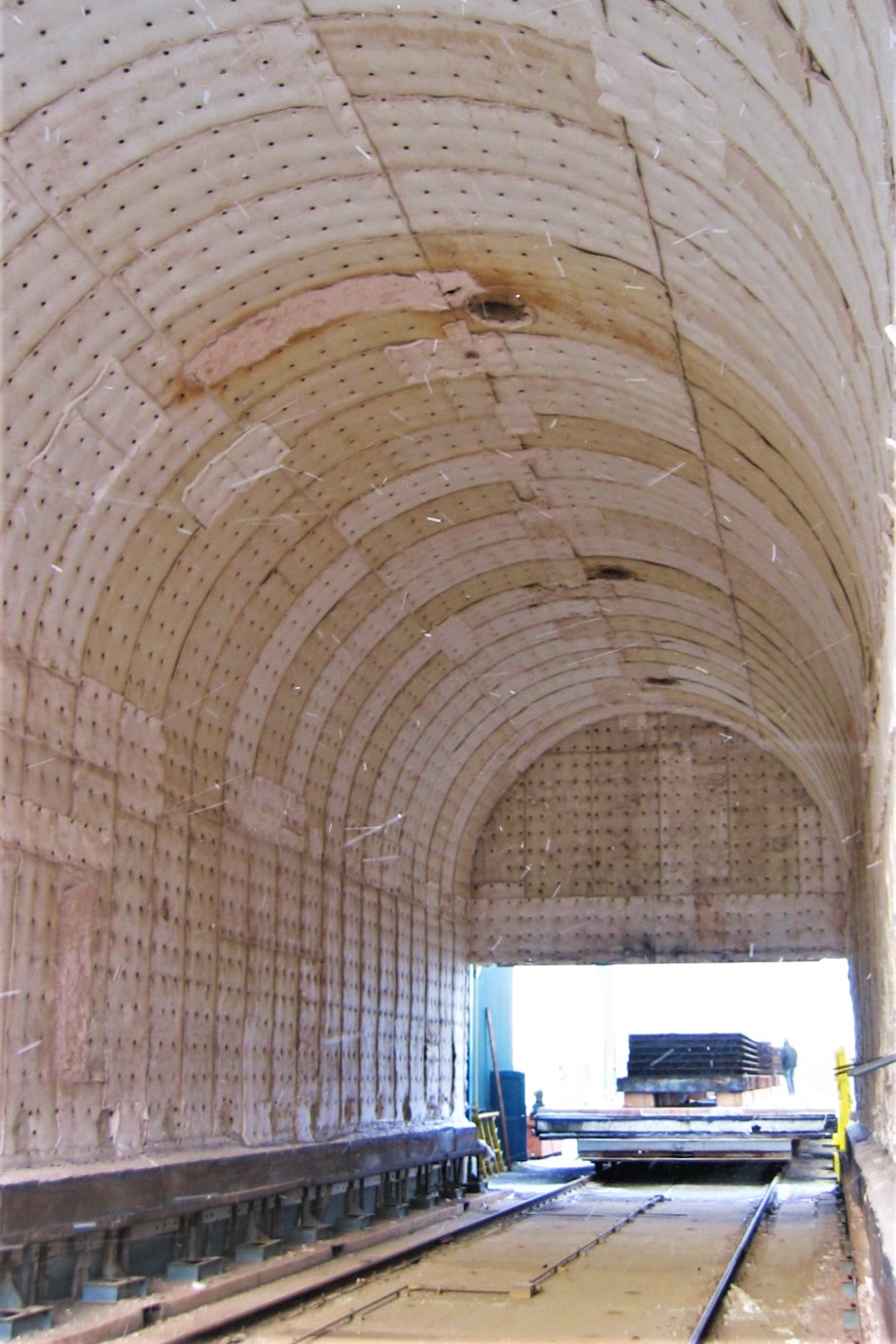
The Firebridge Solution
Using the Six Delta™ Method to gain an optimised perspective, Firebridge identified several performance improvement opportunities. The Six Delta™ Method is a comprehensive approach through a systematic analysis which considers improvements over six interdependent focus areas. This method is data driven by metrics from each focus area which combine to drive a strong business case.
The Six Delta™ focus areas for this project are:
Primary: Energy Consumption – Product Quality – Process Production – GHGe Emissions
Secondary: Safety & Compliance – Equipment Reliability
The Diagnosis and Findings:
- The furnace was fired with the correct air/fuel ratio during high heat requirements (ramp up) but in order to maintain temperature uniformity, the ratio had to be switched to full air/fuel for the soak part of the cycle
- Flue sizing was inadequate resulting in positive furnace pressure causing furnace gases to escape to the corridors around the furnace shell
- Furnace was poorly sealed and produced cold spots inside
- Insufficient refractory on car bottom resulted in excessive heat loss and higher maintenance costs to maintain furnace cars
“Investing in a study will give you the clarity and decision making tools to save hundreds of thousands of dollars in annual energy!”
– Russ Chapman, President, Firebrdige Inc., 2019
Improved results were found across all Six Delta™ focus areas.
Safety & Compliance
- Flue gas escaping into the corridors was eliminated
Quality
- Greater temperature uniformity, faster ramp up time, and still stay within specifications
Productivity
- Furnace can run zones at different temperatures resulting in multiple jobs running at the same time
- Total payback period under 3 years
Energy Consumption
- Converted firing controls to time modulated system (pulse fired)
- Fuel consumption was reduced by 31%
Reliability
- Increased insulation/refractory on car bottom
- Improved car and door seals using sand seals
- Additional car insulation saved $44,000/year
Greenhouse Gas Emissions
- CO2 emissions reduced by 334 metric tonnes/year
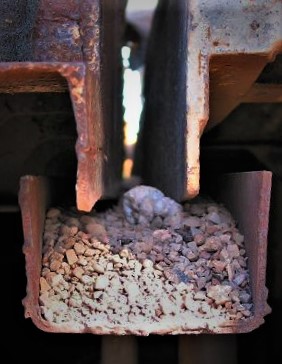
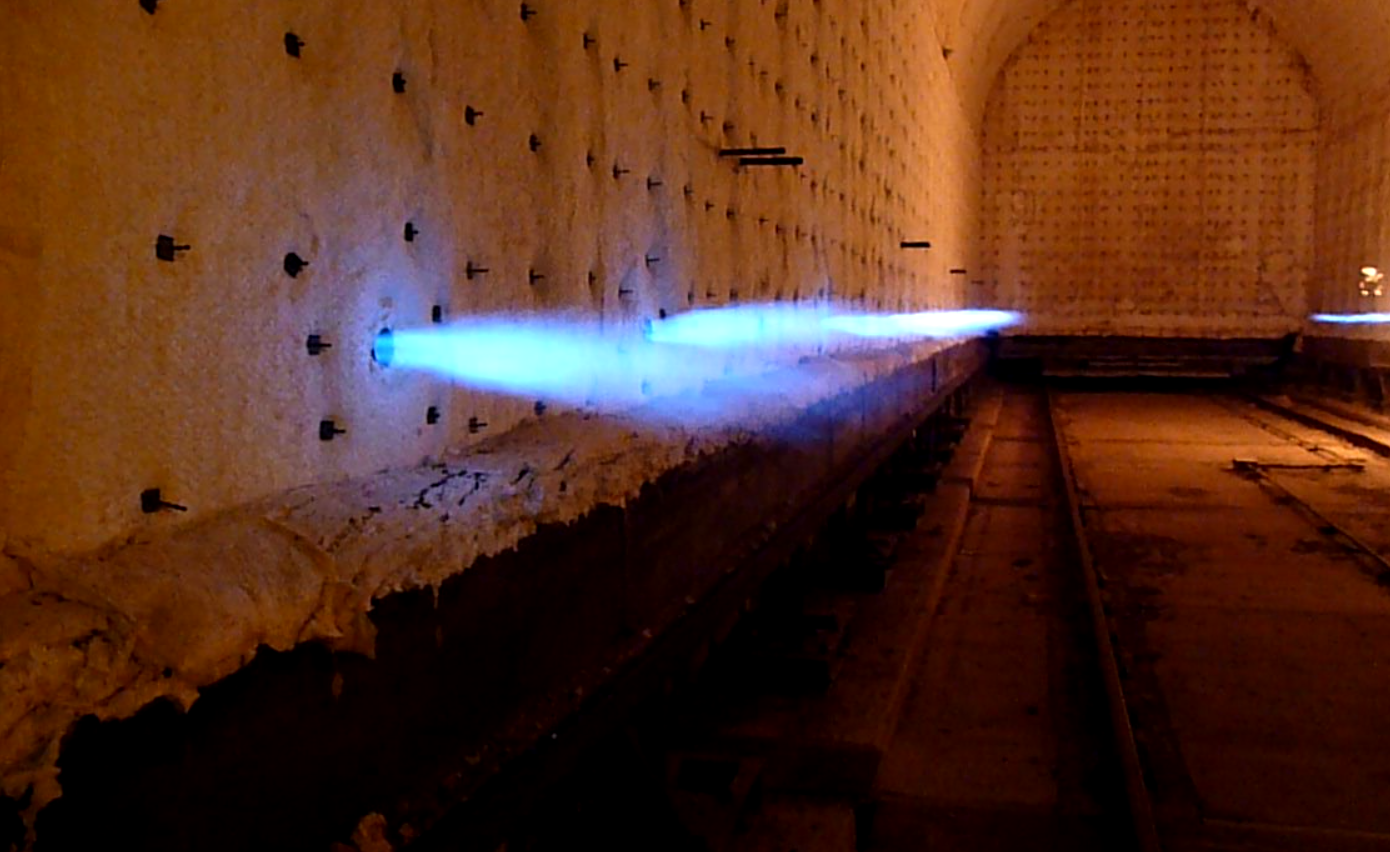
Liked what you read? Stay up to date with new content by Subscribing below!