The Project
This customer’s manufacturing facility produces abrasive steel shot, and uses a natural gas fired retort furnace to harden the shot. In 2016 the original furnace used approximately 386 kWh per tonne of steel shot at a production rate of 2.4 tonnes per hour. Management was concerned that current production, quality, and energy consumption were underperforming compared to industry averages.
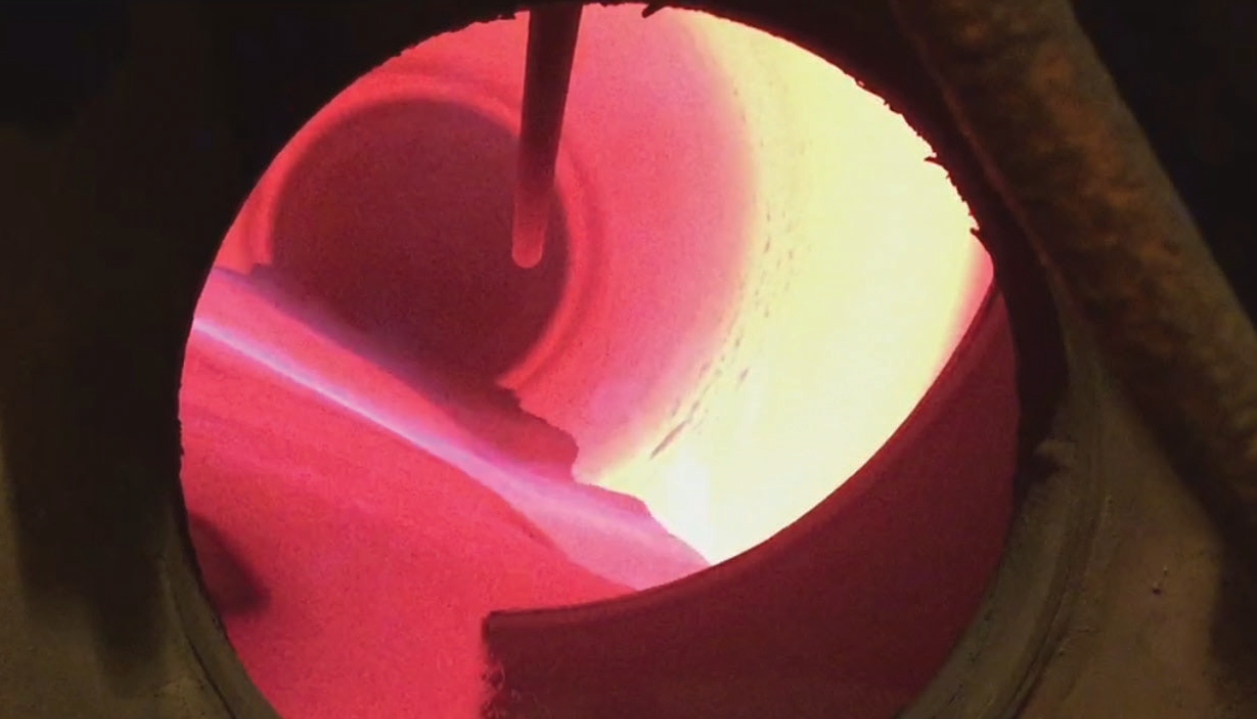
The Firebridge Solution
Using the Six Delta™ Method to gain an optimised perspective, Firebridge identified several performance improvement opportunities. The Six Delta™ Method is a comprehensive approach through a systematic analysis which considers improvements over six interdependent focus areas. This method is data driven by metrics from each focus area which combine to drive a strong business case.
The Six Delta™ focus areas for this project are:
Primary: Energy Consumption – Product Quality – Equipment Reliability – Process Production
Secondary: Safety & Compliance – GHGe Emissions
In July 2018 the original furnace was replaced with a new custom-built furnace engineered by Firebridge.
A key technology upgrade was the use of regenerative flameless oxidation burners. The new burners operate in two modes. The start up mode using traditional flame combustion to bring the furnace to temperature. When the furnace is at temperature the burners switch to the more efficient regenerative mode to achieve the following benefits:
- Consume less natural gas
- Avoids peak combustion temperatures
- Produce a more uniform heat distribution
- Lower thermal stress across the furnace and the retort provides longer service life
- Significant reduction of NOx emissions
![]() Engineered Upgraded Solution |
![]() New Furnace with Regenerative Burners and Safety PLC Control |
“Winoa is extremely pleased with the finished product
Firebridge supplied. We now have the most technologically
advanced furnace and corporate global benchmark for this
process, with improved quality and energy efficiency at over
30% reduction in consumption.”
– Jeff Glaser, V-P Operations, Americas, Winoa, 2019
Improved results were found across all Six Delta™ focus areas.
Safety & Compliance
- The original furnace was not compliant with today’s safety codes. The new furnace meets the current safety codes.
- Existing relay-based controls replaced with safety PLCs.
Quality
- The original furnace produced shot that had a low recovery rate of product that met quality specifications. The new furnace establishes the corporate global benchmark for abrasive shot quality.
Productivity
- The throughput capability has been increased by 33% and now reaches levels of 3.2 tonnes per hour.
Energy Consumption
- A 35% reduction in energy consumption was achieved with the new furnace, to now achieve 250 kWh per tonne of steel shot.
Reliability
- Retort cylinder was engineered to triple the service life from the original design. This was possible due to lower thermal stresses and reduced peak temperature.
Greenhouse Gas Emissions
- Achieved a 35% reduction in GHG emissions.
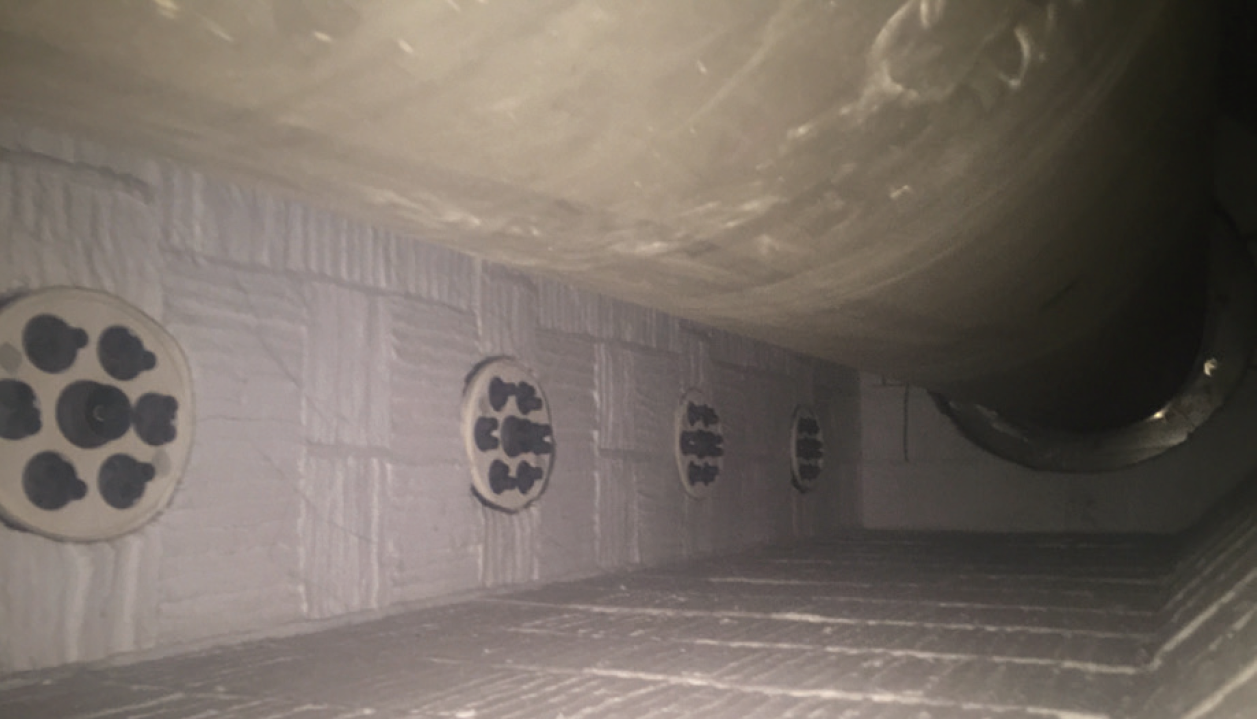
Liked what you read? Stay up to date with new content by Subscribing below!